Environmental Stewardship
As the world’s leading provider of Global Security Solutions, Lockheed Martin maintains the highest standards for ethical business practices and performance in every aspect of its business conduct. The mission of Lockheed Martin’s sustainability program is to foster innovation, integrity and security to protect the environment, strengthen communities and propel responsible growth.
Lockheed Martin builds sustainable supplier capacity by partnering with our supply chain to reduce adverse environmental impacts, to promote human rights, health, safety and ethical behavior, and to enable responsible supplier growth and raise standards. We define Sustainable Supply Chain Management as “management of our supply base to drive affordability and innovation through social responsibility and environmental stewardship.” The objective of Sustainable Supply Chain Management is to ensure alignment of our supply base’s social, ethical, environmental, safety and health responsibilities with Lockheed Martin’s sustainability commitments.
Focus
Our focus on environmental sustainability continues to improve energy efficiency, reduce natural resource usage, and reduce waste. Our focus on social sustainability continues to promote ethics, safety, and human rights. Our focus on governance sustainability continues to progress disclosure, transparency and accountability of management systems, processes and practices. For all aspects, our suppliers represent a key partner in achieving success in sustainability.
Suppliers are encouraged to download a copy of our sustainability supply chain brochure to learn more about our program and how they can become more sustainable to their own operations.
Waste Reduction
Preferred Packaging
Proper product packaging is an integral part of the successful transportation and delivery of any business’s shipped products. Improper packaging can lead to costly problems for both the shipper and the customer, and excessive packaging leads to increases in the flow of waste to landfill. Our objective under this waste reduction focus area is to encourage preferred packaging techniques aimed to reduce packaging waste and minimize environmental impacts whenever feasible.
Preferred packaging materials are typically made from renewable and/or recycled sources; manufactured using clean production technologies and sustainability principles; made from materials healthy in all probable end-of-life scenarios; designed to optimize materials and energy; and effectively recovered and utilized in biological and/or industrial cradle-to-cradle cycles. Some examples of preferred packaging materials include the following:
- Cushioning materials - cellulosic paper, fiberboard and biodegradable bubble wrap
- Bagging materials - reusable bags, paper, bioplastics and recyclable plastics
- Exterior packaging materials - pallets, wood boxes and wood crates
In addition to supporting Go Green reduction goals, improved packaging provides other benefits through the use of renewable and locally sourced materials, as well as the efficient use of transport and storage space. All packaging systems must be compliant with existing contractual and technical (i.e., engineering) requirements and must protect the part to prevent damage.
Lockheed Martin’s sustainable packaging guidelines below can assist our suppliers with proper packaging techniques to prevent damage and reduce packaging waste that is disposed in landfills.
E-Waste Recycling
Lockheed Martin has successfully partnered with our electronic waste (e-Waste) recycling vendors in order to ensure that our used electronics are responsibly managed. Of note, the e-Stewards certification requirement has become a contract requirement for Lockheed Martin’s corporate-approved e-Waste vendors beginning in 2013. E-Stewards-certified recyclers undergo a professional audit every year to guarantee they do not export hazardous recycling byproducts to developing countries, use U.S. prison labor, or dump in municipal landfills. E-Stewards recyclers also ensure that their operations protect both workers and the environment.
We encourage our suppliers to consider using e-Stewards-certified recyclers – to ensure that e-Waste is being responsibly managed.
For information on Lockheed Martin’s commitment to the responsible recycling and stewardship, download the e-Waste brochure below.
Approved Disposal Sites & Vendors
Lockheed Martin-generated waste that under U.S. federal (not solely state or provincial) definitions is hazardous waste must only be manifested to treatment, storage and disposal facilities (TSDFs) identified below that are owned by the National Hazardous Waste Contractors and ultimately may only be treated and disposed of at facilities on the approved vendors list also below.
Conflict Minerals
We adhere to the government’s requirement for companies to publicly disclose their use of conflict minerals originating in the Democratic Republic of Congo or a neighboring country.
Background
In 2012, the Securities and Exchange Commission (SEC) adopted rules implementing the conflict minerals provisions of the Dodd-Frank Wall Street Reform and Consumer Protection Act (Dodd-Frank Act), which require public companies to disclose certain information when a company manufactures or contracts to manufacture products containing Conflict Minerals that are necessary to the functionality or production of those products if the company has reason to believe that the Conflict Minerals may have originated in the Democratic Republic of the Congo (DRC) and the adjoining countries of Angola, Burundi, the Central African Republic, the Republic of the Congo, Rwanda, South Sudan, Tanzania, Uganda and Zambia (the Covered Countries). The term “Conflict Minerals” is defined in the conflict minerals rules and refers to tin, tantalum, tungsten and gold (the Conflict Minerals or 3TG).
Our Policy
Lockheed Martin supports the Dodd-Frank Act’s objective of preventing armed groups in the Covered Countries from benefitting from the sourcing of Conflict Minerals from that region. Substantially all of our products contain 3TG. We are committed to responsible sourcing of materials for our products, including the sourcing of Conflict Minerals, and we expect that our suppliers are likewise committed to responsible sourcing. We recognize that the mining of the Conflict Minerals are an important economic driver in the region and are committed to supporting legitimate mining operations. We have established a due diligence program which follows the framework established by the Organisation for Economic Cooperation and Development (OECD). Due to the enormity of Lockheed Martin’s and its suppliers’ respective supply chains, it will take time for many suppliers to fully adopt program elements that help verify the origin of conflict minerals.
We expect our suppliers to comply with our Supplier Code of Conduct, which is referenced under our Supplier Ethics page and is incorporated into our purchase orders. Our Supplier Code of Conduct includes our expectations that suppliers take steps to determine if their products contain Conflict Minerals and if so, implement supply chain due diligence processes to identify sources of these minerals and support efforts to eradicate the use of Conflict Minerals which directly or indirectly finance or benefit armed groups in the Covered Countries.
We support with financial and human capital industry-wide initiatives, including the Responsible Minerals Initiative (RMI) which assists with our benchmarking and smelter analysis efforts.
We will comply with the requirements of the Dodd-Frank Act, including filing a report annually with the SEC and making such report available on our public website.
For questions regarding our conflict minerals policy, email us or call our Corporate Ethics HelpLine at 1-800-LM-ETHIC.
Specialized Disclosure & Conflict Minerals Report (previous 5 years)
Counterfeit Parts
Our military, government and commercial customers count on Lockheed Martin’s products to work each and every time. Whether it is a satellite, airplane, weapon system or security system, our customers trust that our products will achieve their mission.
The inclusion of sub-standard and unreliable parts in a Lockheed Martin product presents a serious threat to our goal of producing mission critical hardware our customers rely on. One cause of sub-standard and unreliable parts is counterfeit components. Industry reports have increased over the past several years of counterfeit electronic parts infiltrating the aerospace and defense supply chain.
Lockheed Martin requires its suppliers to take steps to eliminate the risk of introducing both counterfeit electronic parts as well as non-electronic parts and materials. We define Counterfeit Work as items that are or contain unlawful or unauthorized reproductions, substitutions or alterations that have been knowingly mismarked, misidentified or otherwise misrepresented to be an authentic, unmodified part from the original manufacturer or a source with the express written authority of the original manufacturer or the current design activity, including an authorized aftermarket manufacturer. Unlawful or unauthorized substitution includes used items represented as new or the false identification of grade, serial number, lot number and date code or performance characteristics.
Industry reports the most common type of counterfeit electronic parts are used, but then modified under uncontrolled conditions and made to appear new. The longevity of aerospace and defense products often exceed the life cycle of commercially available parts. The aerospace and defense industry is particularly vulnerable to this type of counterfeiting scenario. Needed parts may be out of production and no longer available directly from the manufacturers.
With an increasingly complex supply chain, extra diligence must be given to identification, tracking, inspection and management of parts throughout the supply chain to ensure the authenticity of critical parts and materials is not compromised. Lockheed Martin depends on you, our supply base, to be partners with us in our efforts to combat counterfeit part infiltration into our products. Suppliers must have robust counterfeit part control plans that meet and or exceed industry and any applicable government standards. Always reference your Lockheed Martin purchase order for your specific requirements.
The regulatory landscape in regard to counterfeit part prevention continues to evolve. Based on the National Defense Authorization Act of 2012, Section 818, the United States Department of Defense (DOD) released a regulation dictating requirements for counterfeit electronic part detection and avoidance systems. Currently the DOD Federal Acquisition Regulation Supplement (DFARS) requires that contracts with prime contractors and their subcontracts or contain provisions requiring counterfeit prevention processes for DOD suppliers of electronic parts address the following elements:
- Training for the detection and prevention of counterfeit parts.
- Risk based processes for inspection and test to aide in the detection of counterfeit items.
- Processes to abolish the counterfeit parts proliferation.
- Processes that ensure traceability of procured items back to their manufacturer.
- Procurement processes that utilize original component manufacturers or their authorized distributors.
- Reporting to the Government Industry Data Exchange Program suspected counterfeit part incidents and processes to keep suspect or confirmed counterfeit parts quarantined.
- Methodologies to identify suspect counterfeit parts and to work toward confirmation of the counterfeit condition.
- The design, operation and maintenance of systems to detect and avoid counterfeit electronic parts.
- The flow-down of counterfeit detection and avoidance requirements to sub-tier suppliers.
- Processes for keeping continually informed of current counterfeiting information and trends.
- Processes for monitoring GIDEP or other credible sources of counterfeiting information to avoid the purchase or use of counterfeit electronic parts.
- Processes to control and address obsolescence issues.
On Aug. 2, 2016 the DOD issued a final rule under DFARS Case 2014-D005 making further changes to the DFARS to address the detection and prevention of counterfeit parts. The focus of the new rule is on establishing rules for sourcing electronic parts to mitigate the risk of introducing counterfeit parts in the defense supply chain. The rule modifies the existing clause at DFARS 246-7007 Contractor Counterfeit Electronic Part Detection and Avoidance System and adds a new clause at 252.246-7008 Sources of Electronic Parts, both of which are mandatory flow-down provisions. As have past rules on this subject, the rule will impact Lockheed Martin in how it selects suppliers and actions it must take to mitigate counterfeit parts risk and became effective upon its publication.
For the full text of these requirements and changes, we urge our suppliers to review the DFARs 252.246-7007 clause in its entirety which can be found on the Defense Procurement and Acquisition Policy website.
Greater than 95 percent of reported counterfeit issues are the result of procuring parts from distributors or brokers who are not authorized by the Original Component Manufacturer. The simplest and most effective way of combating counterfeit items is to know you are using a manufacturer-authorized supply chain. If you “buy the parts right,” your risk of receiving counterfeit product is minimized. We require Lockheed Martin suppliers to ensure strict procurement policies are in place and ensure traceability for all items that you incorporate into our products back to the manufacturer. Always refer to your Lockheed Martin purchase order terms and conditions, also called “Corpdocs” and the quality clauses for your specific requirements.
Registration, Evaluation, Authorization and Restriction of Chemicals (REACH)
The European Community Regulation (EC) No 1907/2006 concerning the Registration, Evaluation, Authorization and restriction of Chemicals (REACH) entered into force on June 1, 2007, and was enabled in 2008 with the establishment of the European Chemicals Agency in Helsinki, Finland. The regulation aims to better protect human health and the environment by ensuring the risks associated with chemicals are measured and understood. REACH calls for registration of chemicals above specific thresholds that are imported and/or manufactured within the European Economic Area (EEA), chemical disclosure requirements for articles that are imported and/or manufactured within the EEA, and the complete restriction of some chemicals from the EEA altogether.
Lockheed Martin has established a Corporate REACH Program Office within its Global Supply Chain Operations organization that is fully conversant with the requirements of REACH and is leading a corporate-wide implementation structure to ensure compliance throughout the Corporation and within our supply chain.
For questions about REACH within Lockheed Martin, please use the contact button below.
Supplier Sustainability Voluntary Assessment
In order to enhance our understanding of potential sustainability-driven risk and opportunities within our tier one supply base, we conduct an annual supplier sustainability assessment. Suppliers are selected based on a number of criteria: high sales with our company, participation in a current or previous supplier ethics mentoring program, travel and transportation vendors (e.g. airlines), and small businesses with significant spend.
As a result of the assessment, we gain insights and take actions on topics that span the environmental, social, and governance categories. By partnering across functions, we are able to ensure every questions we ask yields a data point that can be acted upon. After analyzing the results, we develop action plans for supplier engagement and our own sustainability performance.
This past year, we expanded the number of recipients, enhanced the questions based on prior year stakeholder feedback, and integrated the applicable survey questions from the International Aerospace Environmental Group (IAEG) industry-wide survey harmonization efforts. The Supplier Sustainability Assessment is promoted in the corporation’s Sustainability Report, GRI and Dow Jones Sustainability Index submittal.
What Can Suppliers Do?
Familiarize yourself with Lockheed Martin’s Sustainability program and our need to account for our sustainability impacts and those of our suppliers
- Assess your company’s alignment with Lockheed Martin’s Supplier Code of Conduct
- Establish a company-wide baseline for carbon emissions, facility energy use, water consumption and waste to landfill (see more information below about Reneway Program)
- Respond to Lockheed Martin requests for sustainability related information, as the need for transparency is increasingly important
- Offer environmentally preferable products that reduce energy, carbon emissions, water usage, and waste output and recommend these products as an option when the conventional equivalent is selected
- Utilize Lockheed Martin’s sustainable packaging guidelines to learn how best to package products in an environmentally friendly fashion
- Work with your Lockheed Martin high-volume sites to institute reusable packaging solutions
- Support future Green Procurement Plan initiatives as they relate to your commodity competencies
- Update your company’s Exostar supplier profile to answer new questions that relate to Sustainability
- Utilize ENERGY STAR’s Guidelines for Energy Management to establish a strategic energy management program.
Reneway Program
The RENEWAY program, founded by Lockheed Martin, provides suppliers across the aerospace and defense industry a runway to take climate action and reduce carbon emissions by accelerating the adoption of renewable electricity. The program provides critical resources and expert consultation for suppliers in any stage of their decarbonization journey to navigate the diverse array of options within the renewable energy market and create a procurement strategy.
Access to support and educational material is free for the industry supply chain through corporate sponsorship of the program. RENEWAY, fosters collaboration and partnership among corporate sponsors and their suppliers, empowering collective impact towards a low carbon future. Aerospace and defense suppliers that join RENEWAY have the unique opportunity to combine electricity purchasing power to form buyers' cohorts and/or explore regional and onsite renewable opportunities. The cohort model creates access to renewable electricity for many suppliers that would not have enough electricity demand to meet the scale needed for affordable purchasing on their own.
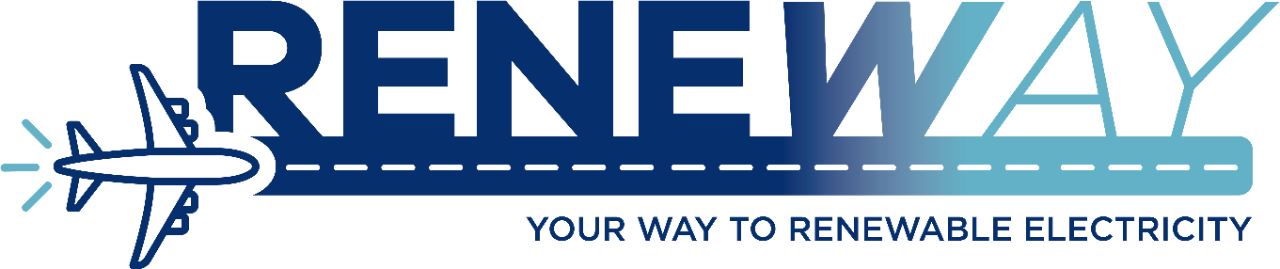